A Isometric Micro Molding, conhecida por sua experiência em micromoldagem por injeção, expandiu seu uso de impressão 3D para apoiar ainda mais o desenvolvimento de dispositivos médicos miniaturizados. Brent Hahn, vice-presidente de desenvolvimento e estratégia de negócios da Isometric, compartilhou o progresso da empresa durante a sessão do IME West 2023 Medtech Theatre, “Uma comparação para microaplicações: peças impressas em 3D, peças moldadas a partir de moldes impressos em 3D e peças moldadas a partir de moldes tradicionais”.
Definindo a micromoldagem como “peças que são uma fração do tamanho de um pellet de resina”, Hahn disse ao público que a Isometric “pode fazer mil peças com um único pellet de resina se não houvesse um corredor”. Peças maiores também podem ser moldadas com microcaracterísticas. Por exemplo, ele descreveu a moldagem de um 3-in. peça com 175 características que medem apenas 25 mícrons cada uma – um quarto da largura de um cabelo humano – usando moldes de metal, em grandes volumes e com alta cavitação. Outro exemplo envolvia peças de micromoldagem com uma proporção de 400:1 e tolerâncias igualmente rígidas.
Além de oferecer micromoldagem, a Isometric pode imprimir em micro 3D peças individuais ou conjuntos completos para prototipagem, bem como inserções de micromolde em impressão 3D para uso em uma base de metal existente para micromoldagem rápida e curta no termoplástico pretendido.
A Isometric “começou há cerca de três anos com uma impressora e agora temos três com resolução super alta e sete impressoras 3D no geral para ajudar nossos clientes em seus processos de desenvolvimento em nosso novo laboratório de inovação”, disse Hahn. Por exemplo, “imprimimos em 3D a espessura de uma peça inteira de 25 mícrons. Isso não é um recurso ou uma parede – é o tamanho total da peça.” Hahn disse que foi um exemplo extremo, mas se a Isometric pode imprimir nesse nível, seu trabalho pode ajudar os engenheiros de projeto a passar rapidamente por várias iterações. A Isometric está no mercado há mais de 33 anos e é especialista em Design for Manufacturability (DfM) e Design for Automation (DfA), e esse feedback é incorporado em componentes impressos em 3D ou inserções de moldes impressos em 3D, para apoiar projetos que podem se tornar altos dispositivos de volumes, acrescentou.
Como exemplos, ele compartilhou uma espessura de parede de impulsor de cateter medindo 50 mícrons que “transiciona para translucidez porque é muito fina” e “microagulhas com raios de ponta de 2 mícrons para nitidez”, disse ele.
“Atingir o nível de mícron de precisão real para que nossos clientes possam ter as peças em mãos tão rápido quanto no dia seguinte, em alguns casos, ajuda os grupos de P&D a terem todos os sinos e assobios para criar o melhor design possível”, continuou ele. “Também reduz os custos de desenvolvimento – você não precisa esperar tanto para experimentar designs diferentes com recursos nítidos e acabamento superficial fino.”
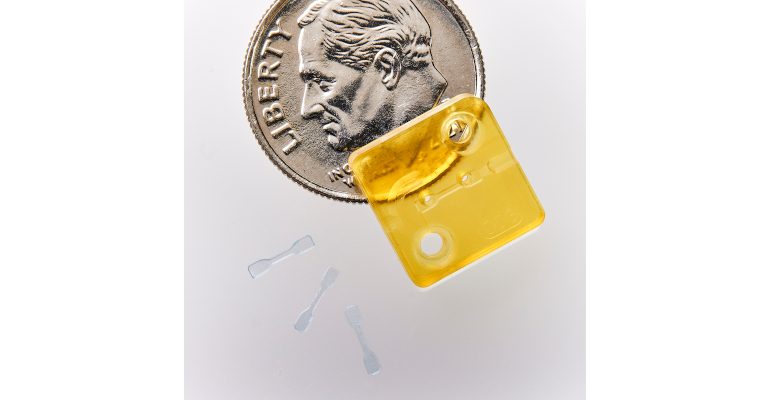
Comparando a Micromoldagem com a Microimpressão 3D
Hahn compartilhou um estudo Isometric conduzido comparando o uso de micromoldagem usando moldes de metal, micro insertos impressos em 3D para moldes de metal e impressão de peças em micro 3D.
Para este estudo comparativo, a empresa imprimiu peças em 3D, inserções de molde impressas em 3D e construiu um molde de metal com oito cavidades para moldar peças com espessura de 25 mícrons (0,001 pol.) a 200 mícrons (0,008 pol.). “Sem querer roubar o brilho desta apresentação, mas fomos bem-sucedidos”, disse ele ao público do IME West. “Todas as oito opções de espessura, incluindo 0,001 pol., puderam ser moldadas nas inserções de molde impressas em 3D e nos moldes de metal.” A impressão micro 3D também foi capaz de imprimir os diferentes tamanhos de peças.
“Estamos entusiasmados em oferecer esta solução de ponta, onde você pode ter o polímero pretendido em suas mãos em uma semana e em alta resolução versus polímero fotossensível impresso em 3D versus o tempo que leva para construir um molde tradicional. Agora, ter uma segunda opção viável de desenvolvimento rápido permite que o cliente faça a escolha certa para o escopo do projeto, com base em tempo, dinheiro e prioridades, como peças únicas ou um grande número de peças”, concluiu.