Quando as grandes montadoras de automóveis querem experimentar e ampliar limites no projeto automotivo, elas se voltam para a Vital Auto, a qual, por sua vez, se volta para um departamento de impressão 3D bem equipado para concretizar estas idealizações.
A Vital Auto, sediada no Reino Unido, é um estúdio de design industrial com ampla experiência em projetos automotivos. A clientela da empresa inclui muitas das principais montadoras, como Volvo, Nissan, Lotus, McLaren, Geely e Tata.
“Os clientes normalmente vêm até nós para tentar ampliar os limites do que é possível com a tecnologia disponível”, disse Shay Moradi, VP de Inovação & Tecnologia Experimental da Vital. Quando os fabricantes não têm tempo para realizar estes experimentos, eles confiam na Vital Auto para transformar ideias, esboços iniciais, desenhos, ou especificações técnicas em uma forma física totalmente concretizada. Uma das ferramentas que a Vital Auto utiliza para criar protótipos de alta-fidelidade e carros-conceito é uma frota de impressoras Form 3L e Fuse 1 3D da Formlabs.
O conceito chinês de EV
Um dos primeiros projetos que a empresa assumiu foi voltado para o conceito de supercarros elétricos chineses NIO EP9, que direcionou a equipe para a produção de protótipos de veículos extremamente realistas e de alta-fidelidade.
Dependendo da solicitação do cliente, a equipe começará em qualquer lugar partindo desde um esboço em um pedaço de papel até um veículo já projetado. A equipe desenvolve carros a partir de uma folha em branco, projeta todos os mainframes, todos os elementos exteriores e interiores, e elementos interativos. Com cinco a 30 pessoas trabalhando em um único conceito, um projeto típico pode levar de três a 12 meses.
Um carro típico de exposição passa por até uma dúzia de iterações de design de núcleo, e dentro delas, pode haver mais iterações de componentes menores até que o design atenda às expectativas do cliente.
“Em nossa indústria, está tudo bem se considerarmos as propriedades virtuais como um meio de avaliar um produto antes que ele chegue ao mercado. Entretanto, acho que sempre haverá um lugar para objetos fabricados fisicamente também. Não há nada que supere a sensação e o sentimento de segurar um objeto em suas mãos com o peso e as proporções corretas, e a dinâmica de como o ambiente físico muda sua percepção sobre esse objeto concreto”, disse Moradi.
Da argila de moagem aos jogos de peças 3D
Enquanto os carros de exposição tradicionais são normalmente feitos apenas de argila de moagem, a equipe também usa fresagem CNC de três e cinco eixos, moldagem manual, modelagem manual de argila, e compósitos GRP. Estes processos tradicionais, entretanto, muitas vezes não são ideais para produzir as peças personalizadas necessárias para conceitos exclusivos.
“Usamos a impressão em 3D desde o primeiro dia. Queríamos introduzi-la em nossos processos de fabricação, não apenas para reduzir custos, mas para dar aos clientes mais variedade com seus designs e ideias”, disse Anthony Barnicott, Engenheiro de Design responsável pela fabricação de aditivos.
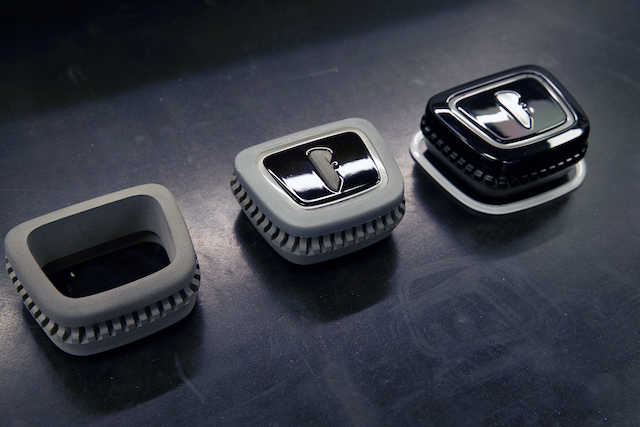
Atualmente, Barnicott opera todo um departamento de impressão 3D, equipado com três impressoras Formlabs 3L estereolitografia de grande formato (SLA), cinco impressoras Fuse 1 de sinterização a laser seletiva (SLS), e 14 impressoras de modelagem de deposição fundida de grande formato (FDM).
“Em termos de capacidade, todas essas impressoras funcionaram 100%, 24 horas por dia, 7 dias por semana, praticamente desde o primeiro dia. Utilizamos essas impressoras para todas as áreas de nossos conceitos e projetos. Normalmente, usaríamos os Fuse 1s para nossas peças baseadas em produção e os Form 3Ls para nossas peças baseadas em conceito”, disse Barnicott.
Projetos complexos realizados a partir de múltiplos materiais
“Usamos as máquinas Form 3L para tudo que seja uma superfície com acabamento de classe A. Assim, normalmente, em um ambiente automotivo, um interior onde você tem peças que não estão sendo aparadas com couro ou Alcântara ou algum tipo de material de tecido. Os materiais Formlabs nos dão um acabamento agradável e suave para nossos pintores trabalharem; podemos usar essas peças diretamente da impressora, diretamente em um veículo”, disse Barnicott.
“O que mais me interessa nas máquinas Form 3L é sua versatilidade, a capacidade de fazer uma troca de material em menos de cinco minutos, e a variabilidade desses materiais – passando de um material macio e flexível para um material duro e rígido para nós não tem preço”, disse Barnicott.
A equipe utiliza as impressoras Form 3L com múltiplos materiais para numerosas aplicações, sendo uma delas a ventilação. “É um desafio comum para nós como um negócio onde os clientes nos abordam com um produto proprietário e querem envolvê-lo em seu próprio projeto. Uma vez, um cliente se aproximou de nós com uma abertura de ar própria de outro veículo que ele desejava ter dentro de seu próprio interior. Utilizamos a tecnologia de escaneamento 3D para reproduzir esta peça digitalmente e depois criamos uma pele externa. Primeiro produzimos isto no material de esboço para testar o projeto e permitir que o cliente o verificasse. De lá, mudamos para o material branco para fabricar uma peça pronta para produção”.
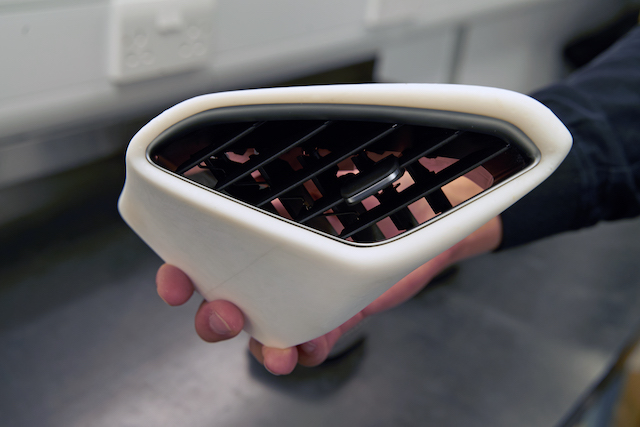
Os pacotes de interruptores são outro exemplo de aplicação do SLA. “Quando trabalhamos com projetos incrivelmente complexos, como pequenos pacotes de interruptores, podemos usar vários materiais para conseguir um produto mecânico que não só funcione corretamente como também possa ser usado em um ambiente do mundo real”, disse Barnicott. Aqui, “combinamos materiais mais duros, como a Resina Tough 2000 para a superfície superior, com os materiais mais leves e mais econômicos para o interior”. A Resina Tough 2000 é o material mais forte e rígido disponível na Formlabs, e simula a resistência e a rigidez do ABS.
As vedações das portas são outra área adequada para SLA. “Normalmente, as vedações de portas para aplicações automotivas podem ser incrivelmente caras de se produzir. Simplesmente não há outra maneira além da moldagem por extrusão para produzi-los”, explicou Barnicott. “Isto não vem apenas com um custo muito grande de ferramentas, mas também com um longo tempo de espera. Fomos capazes de experimentar um dos mais novos materiais da Formlabs, o Flexible 80A. O Form 3L nos permitiu produzir seções desta vedação de porta durante a noite para testar várias geometrias e foi impresso dentro de 50 microns do projeto real”. O Flexible 80A simula a flexibilidade da borracha ou TPU.
Complementando a usinagem CNC com SLS
“O Fuse 1 foi um de nossos primeiros empreendimentos na tecnologia SLS. Estas máquinas produzem peças estruturais muito rapidamente, não apenas para testes, mas para aplicações físicas na maioria de nossos conceitos. Este processo normalmente teria sido feito por usinagem CNC, dentro ou fora do local, dependendo da geometria, e teríamos que esperar de dois a quatro dias para colocar as peças em nossas mãos. O Fuse 1 nos permite cobrir tudo isso no local e ter as peças em nossas mãos, na maioria dos casos, em menos de 24 horas”, disse Barnicott. Ele acrescentou: “Muitas peças internas de automóveis podem ser incrivelmente difíceis de produzir sem seguir a rota tradicional moldada por injeção. Itens como dutos de ar internos e respiradouros – itens que nunca são vistos, mas que requerem um grande custo para serem produzidos. Usamos o Fuse 1 para produzir estas peças. Ele nos permite ser muito mais versáteis com os projetos que colocamos no veículo sem incorrer nos grandes custos que eles normalmente teriam”, disse Barnicott.
“Há certas coisas que você não pode mais classificar como tecnologias emergentes”, concluiu Vital VP Moradi. “A impressão em 3D é uma dessas coisas. É avançada a um ponto em que tudo o que produzimos é suficientemente bom para ser usado na fase final de apresentação, com todas as camadas de fabricação que aplicamos em cima disso. A impressão em 3D passou de quase uma novidade para uma parte absolutamente inseparável do que fazemos”.